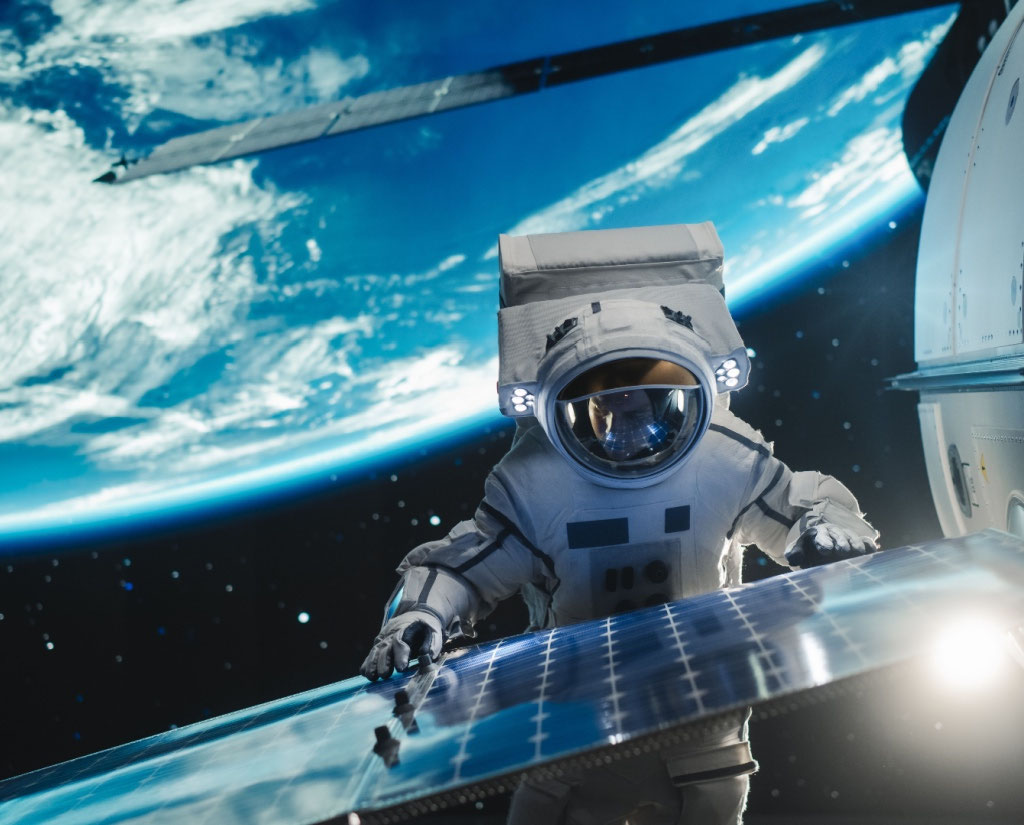
When it comes to the future of manufacturing, self-assembly is the order of the day. Even with the advent of 3-D printing, fashioning objects, buildings and tools can be a time-consuming and tedious process. But if it were one-day possible to create components and materials that could assemble themselves and adjust their configurations based on external conditions, it would not only save us all a ton of time and money, it would also revolutionize the way we live.
In recent years, developments have been made that seeks to generate SA materials using 3-D printing. In this context, they are what is known as 4-D materials – a process where customizable materials are created using a 3-D printer, but which are capable of folding and adjusting their shape at a certain point in time.
The latest in this trend comes from MIT, where researchers at the Self-Assembly Lab have collaborated with Autodesk and Stratasys - two leading companies in the field of 3-D printing hardware and software - to create materials that are not only capable of folding themselves, but also stretching and bending in response to external stimuli.
In a paper which was recently published in Scientific Reports, they describe how such a material could be used to create self-evolving structures that vary over time due to interaction with their environment. Dan Raviv, a postdoc at the MIT Media Laboratory and the lead author on the paper, said the following:
“If a structure is going to change, and curvature appears — like going from a flat domain to something that has effective curvature, such as a mountain — the area is going to change. There’s going to be stretching. Until now, people just considered bending, which leaves the area and lengths the same. Or they did some stretching, but without the ability to control or pre-program it. Now we need to develop new sets of tools to do both.”
Development of the process began last year when Skylar Tibbits - a research scientist in MIT's Department of Architecture who heads the MIT Self-Assembly Lab - invited Raviv and other members of the Media Lab’s Camera Culture group to collaborate on the problem of self-assembly. Their experience interpreting visual data through geometric analysis was seen as essential, since mapping out 3-D models is very similar to mapping out points of color in an image.
The Camera Culture researchers were responsible for developing algorithms to determine how much components of a 3-D object would need to stretch in order to successfully change into another shape. Meanwhile, Tibbit’s group was tasked with figuring out how to make materials that could accomplish this physically.
Along with his team, Tibbits came up with a simple but elegant design for a “linear actuator” - a component that enables segments of printed materials to stretch. In the component, two polymer disks are connected to each other by two bowed strips of a composite polymer. The inner edges of the bowed strips are made from the expanding polymer, and when they absorb water, the strips straighten out.
Experiments have been done in the past where 3-D printers were able to generate pieces of materials that could be assembled by hand and which would then self-fold if immersed in water or heated. But the challenge here was to create something that could be assembled completely and then self-adjust without additional assembly.
After much experimentation to get the parameters just right, they created a self-folding strand that was capable of going from a rigid position to spelling the initials MIT (see image at top and above). This is not the first time that such materials have been created, as the self-folding cube (see video below) will attest. Tibbits was also the one responsible for coining the term 4-D printing, where the fourth dimension is the time it takes the object to assemble.
Similarly, experiments conducted by the University of Colorado, Bolder last year have garnered the attention of SA enthusiasts. Here, Prof. H. Jerry Qi and Martin L. Dunn - of the Singapore University of Technology and Design - created a series of shape-memory polymer fibers that were combined with composite materials as they were being printed.
By carefully controlling the location and orientation of the fibers, they were able to print off items (like the folding blocks pictured with Prof. Qi below) that can fold, stretch, curl or twist in a predictable fashion when exposed to a stimulus such as water, heat or mechanical pressure.
A fascinating field of research, especially when you consider that the inspiration behind it is biological in nature. As the fundamental component of all life, protein molecules are composed of poylpeptide strands of nucleic acids that fold into specific configurations to form the building blocks of different tissues, which in turn perform different functions.
By combining that concept with the world of robotics and manufactured products, researchers are seeking to create structures and objects that are capable of assembling and reassembling on command. In addition, research into programmable biological structures that can adjust and carry out various functions under different types of stimulation is also proceeding apace. In this respect, the building blocks are organic, but the purpose remains the same.
At this rate, we could be embarking upon a future where buildings are composed entirely of components that assemble themselves to form tenements, skyscrapers or houses, and then reorient themselves when they need to to deal with rain, snow, or high winds. The multi-tool could also live up to its name - a single object made up of adjustable robotic bits that change configurations to form different tools on command.
And, looking far ahead, organic technology could eventually be pioneered that would turn all buildings and objects in our world into living, breathing tings, capable of responding to the needs and habits of their users/inhabitants. Dare we dream?
And be sure to see the following videos from MIT and TEDx that deal with 4-D Printing and SA materials:
4-D Self-Folding Cube:
TED Talks: Skylar Tibbits - The Emergence of 4D Printing:
Sources:
- newsoffice.mit.edu/2014/3-d-printed-materials-curve-stretch-1218
- www.selfassemblylab.net/4DPrinting.php
- www.gizmag.com/4d-printing-composite-material/29536/
- www.selfassemblylab.net/ProgrammableMaterials.php
- www.nature.com/srep/2014/141211/srep07422/full/srep07422.html
- www.colorado.edu/news/features/%E2%80%98memory-fibers%E2%80%99-add-fourth-dimension-3d-printing
Image Credits:
- Top Image: MIT
- Linear Actuators: MIT
- Folding Strand: Self-Assembly Lab
- Prof. Qi and 4-D Folding Block: colorado.edu